Introduction to Plate Heat Exchangers
Are you looking for Plate Heat Exchangers the ultimate guide to selecting, designing, and installing plate heat exchangers? Look no further. In this comprehensive article, we’ll walk you through everything you need to know to make an informed decision and ensure a seamless installation. Plate heat exchangers are highly efficient and cost-effective devices that are widely used in various industries.
We’ll provide step-by-step instructions for the installation process, including tips for proper maintenance to extend the lifespan of your plate heat exchanger. Stay tuned to learn the ins and outs of plate heat exchangers, and take your understanding to the next level. Let’s get started on a journey to improved heat transfer efficiency and cost savings.
Understanding Heat Exchangers
Plate heat exchangers (PHEs) are highly efficient and versatile devices used to transfer heat between two or more fluids. They play a critical role in a wide range of applications, from industrial processes to HVAC systems and beyond. What Is a
Plate Heat Exchanger?
At its core, a plate heat exchanger is a compact and efficient heat transfer device. It consists of a series of metal plates that are specially designed to facilitate the exchange of thermal energy between two fluid streams without them coming into direct contact with each other. The key components of a plate heat exchanger include:
Heat Transfer Plates:
These plates are typically made of stainless steel or other materials with excellent heat conductivity. They have intricate patterns of channels and corrugations to create a large surface area for heat exchange.
Gaskets or Brazing:
Depending on the design, the plates are sealed together with gaskets or are brazed together to prevent the mixing of the two fluid streams.
Inlets and Outlets:
Each fluid stream has its own set of ports for inlet and outlet, ensuring that they flow through their respective channels without intermixing.
Advantages of Plate Heat Exchangers
Plate heat exchangers (PHEs) offer numerous advantages, making them a popular choice for a wide range of heat transfer applications. Here are some of the key advantages of plate heat exchangers:
- High Heat Transfer Efficiency
- Wide Range of Materials
- Environmental Benefits
- Diverse Applications
- Reduced Maintenance
- Temperature Control
- Quick Installation
- Low Pressure Drop
- Energy Efficiency
- Minimal Fouling
- Compact Design
- Cost-Effective
- Quick Start-Up
- Customization
- Flexibility
These advantages make plate heat exchangers an attractive choice for many industries and systems where efficient heat transfer is essential. Their ability to save space, reduce energy consumption, and offer cost-effective solutions has contributed to their widespread use in various applications.
Buy Plate heat exchangers (PHE) online from hear – Amazon link
Applications and Industries Plate heat exchangers
Plate heat exchangers (PHEs) find a wide range of applications across various industries due to their high heat transfer efficiency, compact design, and versatility. Here are some of the primary applications and industries where plate heat exchangers are commonly used:
- HVAC (Heating, Ventilation, and Air Conditioning)
- Environmental and Water Treatment
- Pharmaceutical and Biotechnology
- Mining and Minerals Processing
- Food and Beverage Processing
- Petrochemical and Refining
- Marine and Shipbuilding
- Oil and Gas Industry
- Chemical Processing
- Automotive Industry
- Waste Heat Recovery
- Power Generation
- Renewable Energy
- Refrigeration
- Agriculture
Heat Exchangers Calculation excel spreadsheet sheet link.

Plate heat exchangers are versatile and can be customized to suit the specific needs of various applications and industries. Their ability to efficiently transfer heat while maintaining a small footprint and low energy consumption has made them an indispensable component in many processes and systems across the world.
Selection of Plate Heat Exchangers
The selection of a plate heat exchanger (PHE) is a crucial process, as it directly impacts the efficiency and effectiveness of your heat transfer application. To choose the right PHE for your specific needs, you should consider several factors. Here’s a step-by-step guide to selecting a plate heat exchanger:
- Number of Plates and Plate Arrangement
- Define Your Application Requirements
- Compliance with Codes and Standards
- Installation and Space Constraints
- Environmental Considerations
- Plate Material and Gaskets
- Manufacturer Selection
- Plate Size and Type
- Cost Considerations
- Flow Configuration
- Future Expansion
- Fluid Properties
- Pressure Drop
- Customization
- Safety
Once you’ve considered all these factors, you’ll be better equipped to select the most suitable plate heat exchanger for your application. It’s essential to consult with PHE manufacturers or experts to ensure that your choice aligns with your specific needs and provides the best heat transfer performance.
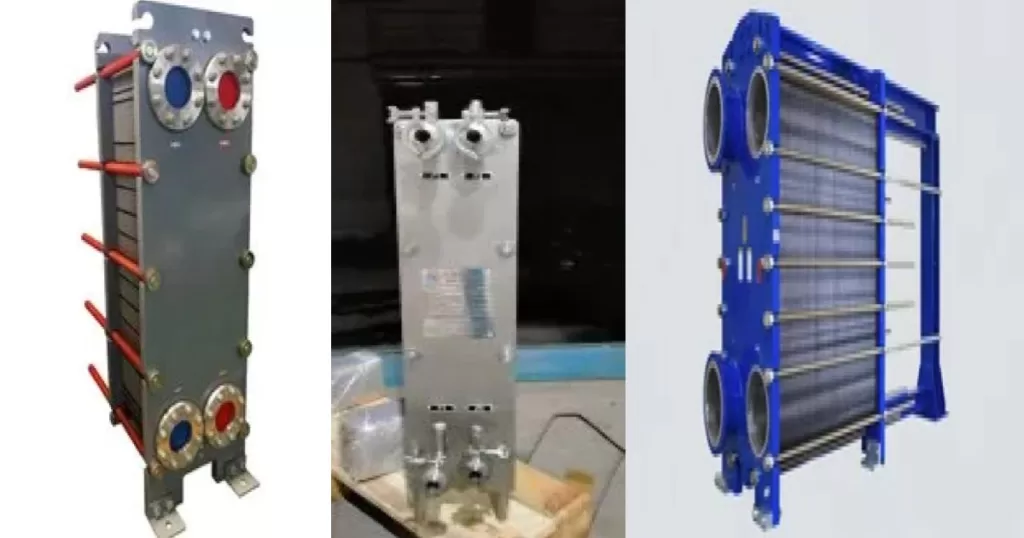
Factors Influencing Selection
Selecting the right plate heat exchanger (PHE) for your application involves considering various factors that influence the performance and effectiveness of the heat exchanger. Here are the key factors that influence the selection of a plate heat exchanger:
- Plate Arrangement and Flow Configuration
- Operating Pressure and Temperature
- Space and Installation Constraints
- Heat Transfer Requirements
- Gasket Material Selection
- Plate Material Selection
- Manufacturer and Quality
- Pressure Drop Tolerance
- Plate Type and Design
- Environmental Impact
- Cost Considerations
- Fluid Properties
- Number of Plates
- Future Expansion
- Safety Features
- Customization
- Flow Rates
These factors collectively influence the selection of a plate heat exchanger to ensure it meets the specific needs of your application while optimizing heat transfer performance and efficiency. Consulting with PHE manufacturers or experts is often advisable to make an informed choice.
Sizing and Capacity Determination
Sizing and capacity determination for a plate heat exchanger (PHE) is a crucial step in the selection process to ensure that the PHE meets the heat transfer requirements of your application. Here’s a guide on how to size and determine the capacity of a PHE:
- Consider Safety and Environmental Factors
- Plate Arrangement and Flow Configuration
- Overall Heat Transfer Coefficient (U)
- Identify Heat Transfer Requirements
- Select Temperature Approach (ΔT)
- Effective Heat Transfer Area (A)
- Determine the Number of Plates
- Plate Efficiency Factor (F)
- Select Plate Size and Type
- Consult Manufacturer Data
- Determine Flow Rates
- Verify the Selection
- Calculate Heat Load
- Check Pressure Drop
Properly sizing and determining the capacity of a PHE is essential to ensure efficient heat transfer in your application. Calculations may vary based on the specific requirements and the type of plate heat exchanger you are using, so consulting with experts and referring to manufacturer data is crucial to making an informed selection.
All required formula is mentioned below (Bottom of the article) with calculation and example.
Choosing the Right Plate Heat Exchanger
Choosing the right plate heat exchanger (PHE) is a critical decision to ensure optimal heat transfer and efficiency in your specific application. Here are the key steps to guide you in selecting the right PHE:
- Understand Your Application Needs:
- Determine the purpose of the PHE: heating, cooling, condensing, or evaporating a fluid.
- Define the required temperature ranges for both the hot and cold fluids.
- Assess Fluid Properties:
- Understand the properties of the fluids involved, such as viscosity, density, thermal conductivity, specific heat capacity, and corrosiveness. This information helps determine the plate and gasket materials.
- Flow Rates and Capacities:
- Specify the flow rates for both the hot and cold fluids. These rates should align with the capacity and heat transfer requirements of your application.
- Temperature Approach (ΔT):
- Determine the acceptable temperature approach, which is the temperature difference between the hot and cold fluids as they pass through the PHE. A smaller ΔT typically results in a more efficient PHE.
- Required Heat Transfer Area:
- Calculate the effective heat transfer area needed to meet your heat transfer requirements. This area depends on the heat load, temperature approach, and overall heat transfer coefficient.
- Plate Material and Gaskets:
- Select the appropriate plate material based on compatibility with the fluids and their properties. Common materials include stainless steel, titanium, and various alloys.
- Choose gasket materials that are compatible with the fluids, operating temperatures, and pressures.
- Plate Arrangement and Flow Configuration:
- Decide on the plate arrangement (single-pass or multi-pass) based on your heat transfer requirements and available space.
- Choose the flow configuration (parallel flow, counterflow, or crossflow) to optimize heat transfer efficiency.
- Pressure Drop Tolerance:
- Assess the allowable pressure drop for your system, taking into account available pumping capacity and system requirements. Ensure that the PHE design aligns with these pressure limitations.
- Customization:
- Determine if you need any customizations, such as additional connections, unique design modifications, or specific dimensions to meet your application’s unique needs.
- Manufacturer Selection:
- Choose a reputable PHE manufacturer or supplier with a track record of producing high-quality heat exchangers.
- Consider factors like product quality, warranty, and after-sales support when selecting a manufacturer.
- Environmental and Safety Considerations:
- Consider the environmental impact of your choice, including energy efficiency and emissions reduction.
- Ensure that the selected PHE design aligns with safety standards and has necessary safety features.
- Cost Analysis:
- Compare the initial purchase cost, operating cost (including energy consumption), and maintenance cost of the selected PHE with alternatives like shell-and-tube heat exchangers.
- Consult with Experts:
- Consult with experts in the field or the manufacturer’s technical support team to ensure that your selection aligns with your specific application’s requirements.
- Validation and Testing:
- Before finalizing the selection, consider running tests or simulations to verify that the PHE can meet the expected performance in your application.
By following these steps and taking into account the unique requirements of your application, you can select the right plate heat exchanger that will deliver efficient heat transfer. Additionally, it will be a cost-effective and reliable solution. Consulting with experts and relying on manufacturer support can be invaluable in the selection process.
Comperision between PHE vs SHE
A comparison between Plate Heat Exchangers (PHE) and Shell-and-Tube Heat Exchangers (SHE) can be done using various factors. Below is a table format comparing these two types of heat exchangers based on several key factors:
Factor | Plate Heat Exchanger (PHE) | Shell-and-Tube Heat Exchanger (SHE) |
Heat Transfer Efficiency | High due to large surface area and turbulent flow. | Lower compared to PHE due to less surface area and lower turbulence. |
Size and Space Requirement | Compact and space-efficient. Suitable for applications with limited space. | Larger and bulkier, requiring more floor space. |
Customization and Scalability | Can be easily customized and scaled up or down by adding or removing plates. | Customization and scalability are often limited, requiring design changes for modification. |
Maintenance and Cleaning | Easier to disassemble and clean, with reduced downtime. | More complex disassembly and maintenance, leading to longer downtime. |
Pressure Drop | Typically lower pressure drop, which can lead to energy savings. | Higher pressure drop may increase pumping power requirements. |
Material Selection | Wide range of plate and gasket materials available, suitable for various fluids. | Typically made of metal tubes and shells, with limited material options. |
Corrosion Resistance | Resistant to corrosion with appropriate material selection. | May require anti-corrosion measures for the shell and tubes. |
Fluid Mixing | Fluids do not mix due to gaskets or brazing, suitable for applications requiring fluid separation. | Fluids can mix within the shell, limiting use in some applications. |
Weight and Installation | Lightweight, easy to install and transport. | Heavier and may require more complex installation. |
Heat Exchanger Cost | Generally more cost-effective, both in terms of purchase price and operating costs. | Typically higher initial purchase cost and operating costs. |
Environmental Impact | Energy-efficient design leads to lower energy consumption and reduced emissions. | Typically consumes more energy, resulting in higher greenhouse gas emissions. |
Flexibility for Temperature Control | Provides precise temperature control due to the ease of adding or removing plates. | Less flexible for precise temperature control without significant design changes. |
Ease of Inspections and Repairs | Easily inspected and repaired, reducing maintenance time. | Complex internal structure can make inspections and repairs more challenging. |
It’s important to note that the choice between PHE and SHE depends on the specific requirements and constraints of your application. PHEs are favored for applications where space is limited, high heat transfer efficiency is required, and where customization and scalability are important. SHEs are more suitable for applications that require high pressure and where heat load changes are infrequent. Consulting with a heat exchanger expert and conducting a thorough analysis of your application needs is essential for making an informed choice.
Plate heat exchangers (PHE) designs formula with calculation and example
Designing a plate heat exchanger (PHE) involves several calculations and considerations to ensure it meets the heat transfer requirements of a specific application. Below are the key formulas and calculations required for PHE design, along with a simplified example:
Heat Load (Q):
Formula: Q = m * Cp * ΔT
Where:
Q = Heat Load (in kW)
m = Mass flow rate of one of the fluids (in kg/s)
Cp = Specific heat capacity of the fluid (in J/(kg·°C) or kJ/(kg·°C))
ΔT = Temperature difference between hot and cold fluids (in °C)
Overall Heat Transfer Coefficient (U):
Formula: U = Q / (ΔTm * A)
Where:
U = Overall Heat Transfer Coefficient (in W/(m²·°C))
Q = Heat Load (in W)
ΔTm = Mean Temperature Difference (in °C)
A = Effective Heat Transfer Area (in m²)
3. Mean Temperature Difference (ΔTm):
Formula for Counterflow: ΔTm = (ΔT1 – ΔT2) / ln(ΔT1 / ΔT2)
Formula for Parallel Flow: ΔTm = (ΔT1 – ΔT2) / ln(ΔT1 / ΔT2)
Where:
ΔT1 = Temperature difference at one end (in °C)
ΔT2 = Temperature difference at the other end (in °C)
4. Effective Heat Transfer Area (A):
Formula: A = Q / (U * ΔTm)
5. Number of Plates (N):
Formula: N ≈ (A / Ap)
Where:
N = Number of Plates
A = Effective Heat Transfer Area (in m²)
Ap = Heat Transfer Area per Plate (in m²/plate)
Plate Efficiency Factor (F):
Typically, F is assumed to be around 0.85 for most plate heat exchangers.
Adjust the heat load calculation by dividing it by F: Q = Q / F
Example:
Suppose you have a plate heat exchanger application where you need to heat 500 kg/s of water from 50°C to 70°C using steam with a mass flow rate of 0.1 kg/s and a specific heat capacity of 2 kJ/(kg·°C). Calculate the required heat load.
Calculate ΔT:
ΔT = Final Temperature – Initial Temperature
ΔT = 70°C – 50°C = 20°C
Calculate Q:
Q = m * Cp * ΔT
Q = 500 kg/s * 2 kJ/(kg·°C) * 20°C = 20,000 kW (20 MW)
In this example, the heat load (Q) is 20,000 kW, which is the amount of heat needed to heat the water from 50°C to 70°C.
This includes determining the optimal number of plates and the necessary effective heat transfer area to meet specific application requirements.
Download PDF FILE FROM HERE – LINK