Pressure Vessels: Introduction
A pressure vessel is a closed container designed to store gases or liquids at a pressure more or less than the outside (ambient) pressure. Pressure vessels play an important role in industries, such as chemical, petrochemical, and manufacturing, where processes require controlled pressure environments. There are many safety standards that have to be followed during the design and fabrication of pressure vessels to ensure the integrity of the vessel and prevent potential hazards. These vessels come in many shapes and sizes, like simple cylindrical tanks, sparical and other each tailored to specific operational requirements. Basically this is consider under the cotegory of static equipments.
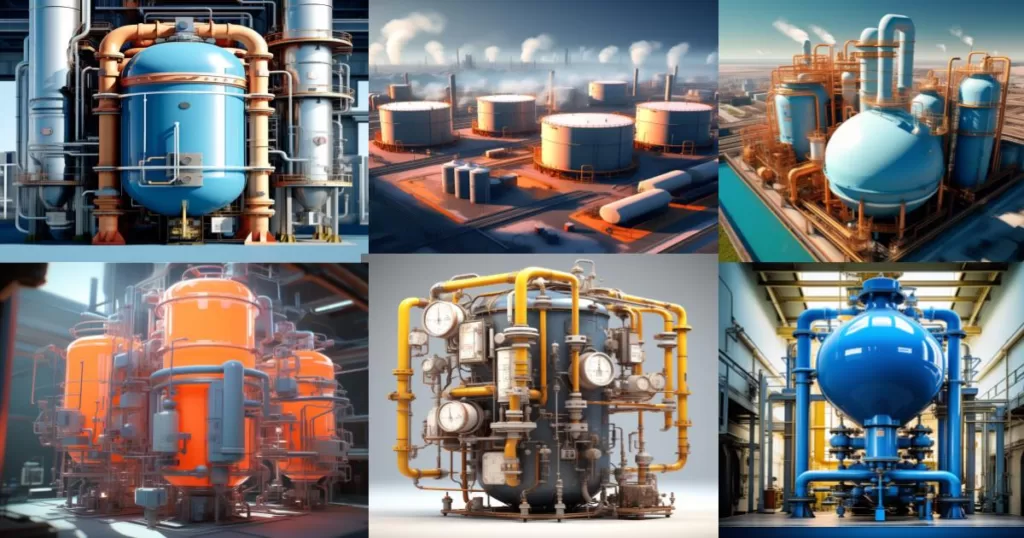
Definition of a pressure vessel |Pressure Vessel Meaning:
Imagine a pressure vessel as a container that holds stuff (like air, gas, or liquids) under pressure, sort of like a soda can, but much stronger.A pressure vessel is a container designed to hold gases or liquids at a pressure substantially different from the ambient pressure. These vessels are built to withstand the internal pressure and ensure the safe containment of the substances they hold.
Pressure Vessel Standards:
Pressure vessels are subject to strict standards and regulations to ensure their safety. Standards provide guidelines for designing, manufacturing, and inspecting pressure vessels. Organizations like the American Society of Mechanical Engineers (ASME) and other regulatory bodies set these standards to ensure the reliability and safety of pressure vessels.
Pressure Vessel Function: Common applications of pressure vessels
The function of a pressure vessel is to contain and manage the pressure of the inside servics fluid. These are used in many industries for indivisual purposes. For example:
- Oil and Gas: Vital for storing and transporting petroleum products.
- Aerospace: Used in spacecraft for storing and handling propellants.
- Automotive: Pressure vessels in airbags enhance safety in vehicles.
- Water Treatment: Applied in water purification processes and storage.
- Nuclear Industry: Used for containment in nuclear reactors for safety.
- HVAC Systems: Employed for refrigerant storage in air conditioning units.
- Pharmaceuticals: Crucial for manufacturing drugs and pharmaceutical products.
- Power Plants: Employed in boilers to generate steam for electricity production.
- Chemical Industry: Used for chemical reactions and storage of volatile substances.
- Food Processing: Utilized for sterilization and cooking in large-scale food production.
Pressure vessel act india | Pressure vessel factories act 1948
Pressure Vessel Act in India, also known as the Pressure Vessel Factories Act of 1948, is a set of regulations aimed at ensuring the safety of pressure vessels used in various industries. Let’s break down the key points in a simpler understanding of this act Purpose, Licensing and Registration, Safety Standards, Inspections and Testing, Certification, Worker Safety, Record Keeping, Penalties for Non- Compliance, Amendments and Updates.
Color codes on vessels
To ensure easy identification, industries use color codes on vessels. Remember, It helps them quickly understand what they’re dealing with and take the necessary precautions.
- Silver or Metallic Colors: Sometimes, pressure vessels are left with their natural metallic color or covered in silver paint.
- Red: Red is a sign of fire and danger! it means the contents inside are flammable or hazardous.
- Blue: Usually signifies compressed air, which is common in many industrial processes.
- Yellow: This color often indicates the vessel’s external surface. Yellow doesn’t mean there’s pressure inside.
- Green:Green color, it’s often associated with non-corrosive liquids.
Harmonized System Nomenclature (HSN code)
Harmonized System Nomenclature (HSN code) for pressure vessels fall under HS code 8419. This code is part of the broader category for machinery, plant, or laboratory equipment. Pressure vessels are further detailed in the HS code 84198910. This sub-code specifies that it includes pressure vessels, reactors, columns, towers, or chemical storage tanks.
Pressure vessel diagram
Pressure vessel internal parts | Vessel parts name | Components of a pressure vessel
1 | Skirt: – Support structure for the vessel. | Welds: – Joints connecting different parts. |
2 | Head: – Curved end caps of a pressure vessel. | Dip Tube: – Guides fluid to a specific level. |
3 | Shell: – Main cylindrical body of the vessel. | Gasket: – Sealing material between components. |
4 | Flange: – Circular connection point for piping. | Jacket: – External layer for temperature control. |
5 | Baffles: – Plates to control fluid flow inside. | Pressure Relief Valve: – Releases excess pressure. |
6 | Impeller: – Rotating device for fluid movement. | Legs: – Additional support for horizontal vessels. |
7 | Thermowell: – Enclosure for temperature sensors. | Vent: – Allows air or gas to escape under pressure. |
8 | Manifold: – Distributes fluid to different parts. | Condenser: – Device for converting vapor to liquid. |
9 | Agitator: – Device for stirring or mixing contents. | Support Ring: – Reinforcement for the vessel bottom. |
10 | Supports: – Structural elements to hold the vessel. | Instrumentation: – Devices for monitoring and control. |
11 | Lifting Lugs: – Attachments for hoisting the vessel. | Level Indicator: – Displays fluid height in the vessel. |
12 | Manway: – Access point for inspection and maintenance. | Reboiler: – Generates vapor for distillation processes. |
13 | Nozzle: – For pipes or instruments to connect. | Catalyst Bed: – Holds material to facilitate reactions. |
14 | Internals: – Internal components like trays or packing. | Sight Glass: – Transparent window for visual inspection. |
15 | Reinforcement Pads: – Extra material for added strength. | Hemispherical Bottom: – Curved base for even stress distribution. |
Working principles of pressure vessels | How pressure vessels work
The working principles of pressure vessels are crucial for their safe operation, considering their verstile use in storing and transporting of gases or liquids under high pressure. One fundamental concept is pressure containment, wherein these vessels are constructed using robust materials capable of withstanding internal pressures. The thickness of the vessel walls is carefully designed to resist forces exerted by the internal pressure, taking into account factors such as corrosion and stress concentration.
To maintain the integrity of pressure vessels, regular inspections and proactive maintenance are essential. Thorough inspections help identify signs of damage, wear, or potential failure, enabling timely repairs or replacements. This approach significantly reduces the risk of accidents and ensures the continued safe operation of the vessels.
Types of pressure vessels
Pressure vessels are containers designed to hold gases or liquids at a pressure different from the ambient pressure. They are widely used in various industries for storing and transporting substances under pressure. There are several types of pressure vessels, each designed for specific applications. Here are some common types:
- Spherical Vessels: Spherical pressure vessels have a spherical shape, which allows them to distribute internal pressure more efficiently. This design is often used for high-pressure gas storage.
- Cylindrical Vessels: Cylindrical pressure vessels come in various forms, such as cylindrical shells with dished ends. They are commonly used for a wide range of applications, including storage of liquids and gases.
- ASME Pressure Vessels: The American Society of Mechanical Engineers (ASME) provides codes and standards for the design, fabrication, inspection, and testing of pressure vessels. ASME pressure vessels must meet specific criteria to ensure safety and reliability.
- Boilers: Boilers are a type of pressure vessel used to generate steam for various industrial processes and power generation. They typically consist of a cylindrical shell with flue tubes or fire tubes.
Heat Exchangers:
Heat exchangers are vessels designed for the transfer of heat between two fluids. They play a crucial role in various industries, including chemical processing, power generation, and HVAC systems.
- Piping Systems: While not traditional vessels, piping systems are essential for transporting fluids under pressure. They include pipes, fittings, and valves and are critical components in many industrial processes.
- Pressure Vessels for Refrigeration: Pressure vessels are also used in refrigeration systems to store and regulate refrigerants. These vessels are designed to withstand the pressures associated with refrigeration processes.
- Composite Pressure Vessels: Composite materials, such as carbon fiber reinforced polymers, are increasingly being used in pressure vessel construction. These vessels are lightweight and have high strength, making them suitable for specific applications.
- LPG (Liquefied Petroleum Gas) Tanks: LPG tanks are pressure vessels designed to store liquefied petroleum gas. They are commonly used for residential, commercial, and industrial applications.
- Cryogenic Vessels: Cryogenic vessels are designed to handle extremely low temperatures, typically below -150 degrees Celsius (-238 degrees Fahrenheit). They are used for the storage and transport of liquefied gases like liquid nitrogen, oxygen, and LNG (liquefied natural gas).
These are just a few examples, and pressure vessels come in various shapes and sizes to meet the specific requirements of different industries and applications. It’s crucial to adhere to relevant standards and codes to ensure the safety and integrity of pressure vessels.
PRESSURE VESSEL HEAD TYPES

Types of Pressure Vessel Head Designs:
Pressure vessels are crucial components in various industries, and the choice of head design plays a significant role in their performance and functionality. Here are some common types of pressure vessel head designs:
- Flat Heads: Simple and cost-effective design, Suitable for low-pressure applications and Easy to manufacture and inspect.
- Spherical Heads: Ideal for high-pressure applications, Distributes stress uniformly and Offers excellent structural integrity.
- Ellipsoidal Heads: Provides better performance under pressure compared to flat heads, Commonly used in many industries and The most efficient shape for minimizing stress concentration.
- Hemispherical Heads: Offers good structural integrity, Ideal for high-pressure vessels and Reduces stress concentrations compared to flat heads.
- Tori conical Heads: Combines the advantages of torispherical and conical heads, Suitable for high-pressure and temperature applications and Efficient stress distribution.
- Conical Heads: Simple design with reduced manufacturing costs, Suitable for low-pressure vessels and Offers ease of access for maintenance.
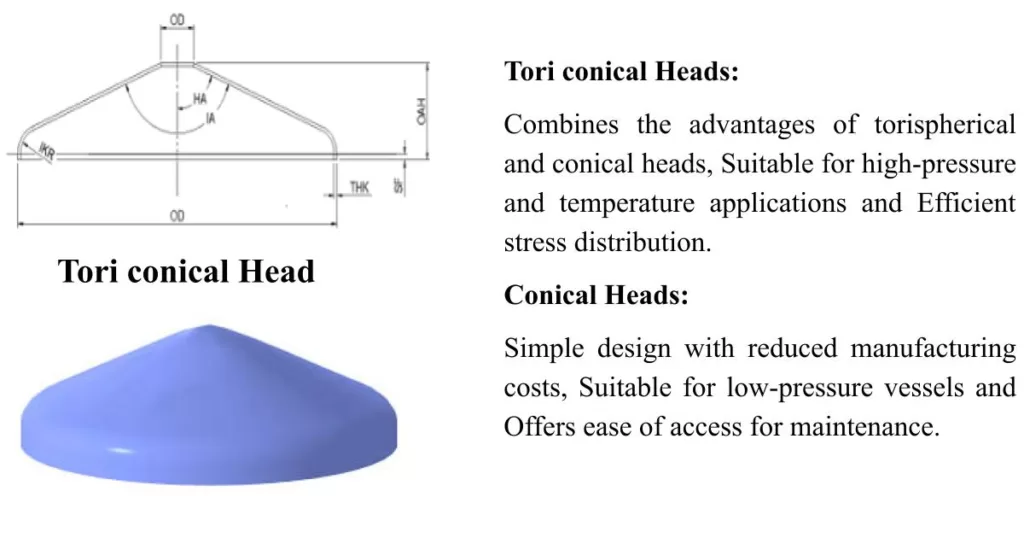
- Dished Heads with Flanges: Enhanced strength and rigidity, Commonly used in applications where additional openings are required and Facilitates easy connections to other components.
- F&D (Flanged and Dished) Heads: Offers a combination of flanged and dished shapes, Suitable for moderate to high-pressure applications and Provides structural stability.
- ASME Flanged and Dished Heads: Compliant with ASME standards, Commonly used in pressure vessels that require ASME certification and Ensures safety and reliability.
- Cone Heads: Simple and economical design, Commonly used in small vessels and horizontal tanks and Provides good drainage capabilities.
TYPES OF DISH END
Dish ends, also known as dished heads or tank heads, are the curved components that form the ends of a cylindrical pressure vessel. Here are some common types of dish ends:
Torispherical Dish Ends: A combination of a toroidal shape and a spherical shape. Efficient for withstanding pressure. Commonly used in a variety of applications.
Ellipsoidal Dish Ends: Provides good efficiency and pressure distribution. Commonly used in medium to high-pressure vessels. Meets ASME standards.
Hemispherical Dish Ends: Spherical in shape, offering uniform stress distribution. Suitable for high-pressure applications. Provides structural stability.
Conical Dish Ends: Conical shape for simplicity and cost-effectiveness. Ideal for low-pressure vessels. Facilitates easy drainage.
Flat Dish Ends: Simple and economical design. Suitable for low-pressure and vacuum applications. Provides easy fabrication and inspection.
Pressure vessel head and dish end types is crucial for designers in ensuring the safety and efficiency of pressure vessels in various industrial processes.
Selection of pressure vessel
The selection of pressure vessel parameters is a critical aspect of designing a vessel that meets the specific requirements of a given application while ensuring safety, reliability, and compliance with relevant standards. Here are key parameters to consider during the selection process:
- Design Pressure: The maximum pressure the vessel is expected to withstand during normal operation. Determined by the process requirements and industry standards.
- Design Temperature: The highest temperature the vessel is expected to encounter during normal operation.
- Influences material selection and thickness.
- Material Selection: Choose materials compatible with the process fluid, temperature, and pressure.
- Consider factors such as corrosion resistance, mechanical properties, and cost.
Vessel Geometry:
Determine the vessel shape, considering factors like head type, diameter, and length. Choose a design that optimizes stress distribution and minimizes material usage.
- Corrosion Allowance: Account for potential corrosion over the vessel’s service life. Add an extra thickness to the vessel walls to compensate for corrosion effects.
- Welding and Fabrication Considerations: Select appropriate welding methods and procedures. Consider fabrication limitations and requirements for inspection and testing.
- Hydrostatic Test Pressure: Determine the pressure at which the vessel will be tested for strength and integrity. Typically a percentage higher than the design pressure.
- Nozzle Size and Placement: Consider the size and location of nozzles for inlet, outlet, and other connections.
- Ensure they meet process requirements without compromising structural integrity.
- Flange Ratings and Connections: Select appropriate flange ratings for connections. Ensure compatibility with process piping and equipment.
- Insulation and Coating: Specify insulation materials to control heat transfer. Choose coatings or linings for corrosion protection.
- Code Compliance: Ensure compliance with relevant codes and standards (e.g., ASME Boiler and Pressure Vessel Code). Consider jurisdictional regulations and specific industry standards.
- Safety Factors: Apply safety factors to account for uncertainties and potential variations in operating conditions. Consider factors such as material properties, fabrication tolerances, and loading conditions.
- Fatigue Analysis: Evaluate potential fatigue effects, especially in cyclic loading conditions. Consider the number of cycles and stress ranges.
- External Loads and Supports: Account for external loads, such as wind, seismic, or thermal expansion. Design appropriate supports and foundations.
- Maintenance Considerations: Design for ease of inspection, maintenance, and repairs. Consider accessibility to critical components.
- Documentation and Certification: Prepare detailed engineering drawings, specifications, and documentation. Ensure the vessel meets certification requirements and standards.